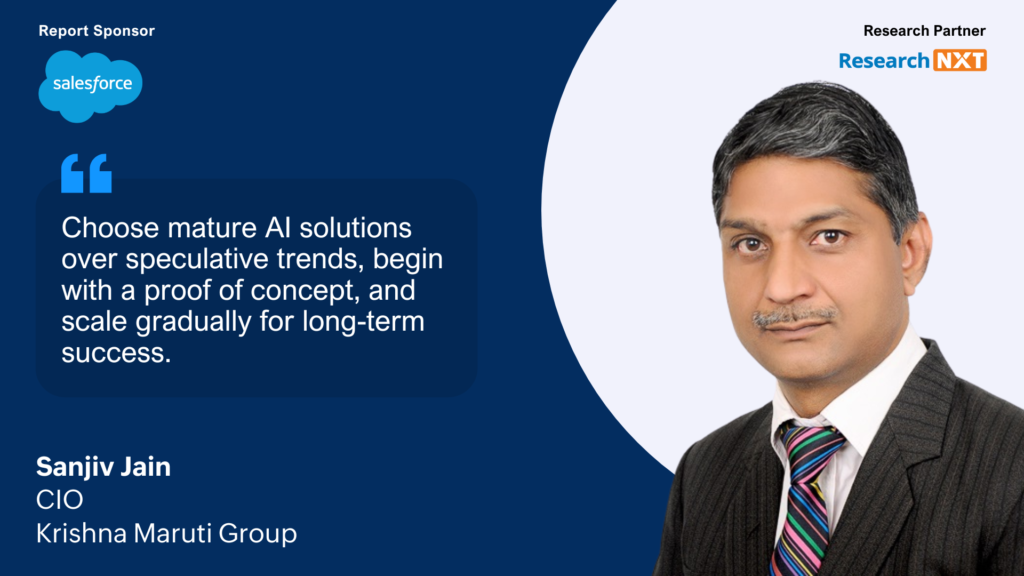
AI-Led Transformation in Automotive Manufacturing
Sanjiv Kumar Jain, Group CIO at Krishna Maruti Group, shares insights on leveraging AI in automotive manufacturing, driving digital transformation, and ensuring data security. With over 30 years of experience, he discusses the adoption of AI for predictive maintenance, machine vision, and digital twins, along with the challenges of integrating AI in a traditional manufacturing setup.
Key Highlights from the Interview
- AI-Driven Manufacturing Innovations: Adoption of machine vision for quality control, predictive maintenance using IoT, and AI-powered workforce training with AR/VR.
- Data Governance & Security: Implementation of zero trust security models, multi-factor authentication, and robust data governance frameworks to protect AI-driven insights.
- Challenges in AI Adoption: Overcoming legacy system constraints, high initial investments, and workforce skill gaps to drive digital transformation.
- Emerging AI Trends: AI-powered supply chain automation, digital twins for process optimisation, and generative design for product innovation in automotive manufacturing.
- Measuring AI Impact: Monitoring machine utilisation rates, defect reduction, cost savings, and predictive analytics to assess AI’s effectiveness.
- Responsible AI Practices: Ensuring explainable AI, unbiased decision-making, and sustainability-focused AI adoption in manufacturing operations.
- AI Implementation Strategy: Start with the problem, not the technology—run proof of concepts, scale gradually, and optimise AI models for long-term success.
“Start with the problem to be solved, not the technology to be applied. Choose mature AI solutions over speculative trends, begin with a proof of concept, and scale gradually for long-term success.”
Can you share your professional journey and your current responsibilities as the Group CIO of Krishna Group?
Sanjiv: I completed my post-graduation in Computer applications. Having many certifications in IT domain to keep updated on technology trends, and also a certified IT security auditor.
Having diversified and rich experience of more than 30+ years in driving initiatives in IT Strategy, implementing most of all renowned ERP’s, IT Security, Business continuity planning and IT Infrastructure designs, Digital transformation, Industry 4.0 implementation with Automation of shop floor in manufacturing, power, Infrastructure and shipping domains.
Received several prestigious recognitions at IDC Insights Awards, IDG CIO 100 Award, CIO SAMMAN by CIO & Leader, BW CIO Award, ET VIO Award, Magnificent CIOs of India Award, CIO POWER LIST recognition, Cyber Smart CIO Award, Cloud Champs award by CIO Axis and many more.
Panellist in various forums in manufacturing summits, ET CIO, 9dot9 Media, Bitstream Media, Polycom, CXOTV, Dun & Bradstreet, UBS Forum, IBM Think teal, Fuelling the Future by Microsoft and Redington to name some and many more
With Krishna Group Leading organisation-wide technology initiatives and driving Industry 4.0 adoption through automation of processes. use of AI through AR/VR projects, AI adoption for product inspection, Integrating the Machine for real-time monitoring and predictive maintenance initiatives, and Creating Data visualisation for better decision-making for top management with data enabled decisions. Inhouse MES (Manufacturing Execution System) implementation for sequence manufacturing and JITs FG creation with full traceability from start to end. Full proofing data security for the organisation-wide data assets along with keeping the lights on for routine IT applications and uptime of the LAN & WAN setup using SDWAN and cloud adoptions.
How has your leadership role evolved with the growing influence of technology in the manufacturing industry?
Sanjiv: CIO’s role has evolved from keeping the Light’s on to an IT enabler and strategic partner with business to drive business value through the adoption of industry-specific right technology to maximise company-wide success to bring business efficiency. Real-time process monitoring for faster and data driven decision making, building an agile organisation embracing automation and business transformation, keeping in mind the internal and external customer’s needs.
Read More
How is AI currently being leveraged in your organisation’s manufacturing operations, such as improving supply chain efficiency, quality control, or predictive maintenance?
Sanjiv: As AI is evolving day by day, we at Krishna group are also adopting the same for Quality control using camera-based/computer vision, which can detect minor abnormalities that might otherwise go unnoticed, thereby reducing waste and ensuring high-quality output in the manufacturing process, Use of AI for predictive maintenance with the use of IOT for monitoring machine behaviour and parameters, use of AR/VR for manpower training on various aspects are some of the initial initiative undertaken and with fruitful results as he application stabilise we will horizontally deploy in other plants with further enhancements and faster deployments.
In your view, what are the most impactful areas within the automotive manufacturing industry where AI adoption can drive significant transformation?
Sanjiv: AI is driving innovation at every turn in the automotive manufacturing industry with OEM it is different with component manufacturers it is different, but AI is transforming how vehicles are produced, right from operations to service, predictive maintenance, autonomous driving, ADAS, supply chain automation, fleet management, providing customer experience automotive companies are leveraging AI to enhance efficiency, safety, and customer experience using AI/ML, AV/VR, digital twins. Component manufacturers can use it for increasing operational efficiencies through automated training, Computer / Machine vision systems can automatically inspect and identify defects or anomalies in products during the manufacturing process, ensuring consistent quality control and leading to waste reduction. Real-time monitoring improves the machine’s availability to sweat the assets to bring down the capex.
How do you ensure the availability and accuracy of data to enable AI-driven decision-making in manufacturing processes?
Sanjiv: AI-driven decision-making in manufacturing processes involves a lot of data cleansing, preprocessing, and augmentation. Once data accuracy is achieved robust evaluation metrics need to be in place to assess the performance of AI models.
With more and more digital dependency, there is a need to maintain high data quality by protecting it from unauthorised access and potential corruption. The concept of CIA (Confidentiality, Integrity and Availability) has to be on top as the dependency on the data increases and any disruption can bring down the whole operations.
Hence, we are building a robust data governance framework to define data quality standards, processes, and roles. Zero trust data security implementation with multifactor authentication are some technologies we are exploring for further fortification.
What role does data integration across departments (e.g., production, supply chain, and customer service) play in supporting AI and analytics initiatives?
Sanjiv: Data integration is crucial & essential because it consolidates information from siloed sources into a unified, coherent and accurate information view. It effectively solves the challenge of handling data from multiple providers it breaks down data silos, ensuring that all parts of the organisation have access to consistent and accurate data. Thus enabling overall data quality for a smooth flow of information and improved analytical capabilities that foster better decision-making. AI can only give the right insights or make informed decisions based on authentic data only.
What metrics or KPIs do you prioritise to measure the effectiveness of AI-driven initiatives, such as improvements in efficiency, cost reduction, or quality enhancements?
Sanjiv: With quantification of tangible and intangible benefits of AI projects with real-time monitoring, we measure the efficiencies, optimisation of machine utilisation (through machine running, idle time, breakdowns, tool change time monitoring), energy consumption, traceability and defect analysis, we get quantity enhancements which leads to cost reduction and better customer experience. With AI-driven training and machine maintenance, turnaround times can be improved; AI can contribute to safety and ESG implementations going forward.
How do you evaluate the ROI of implementing AI technologies in operations and supply chain management?
Sanjiv: First and foremost is adoption rate followed by employee experience and ease of use, performance of the AI model, how many false positives, if customer-facing application than customers experience like quality improvements in product delivered, improvement time of delivery on designs, product improvements. Better monitoring and planning of material flow in the whole value chain leads to JIT Inventory, visibility of material in transit, and quality of material received with integration with a partner for inline production and quality monitoring.
What have been the key challenges in adopting AI technologies in a traditional manufacturing environment, such as talent readiness, legacy systems, or cultural resistance?
Sanjiv: One of the primary challenges is the high initial cost associated with AI technology, making investing in hardware, software and infrastructure significantly critical.
Limited use cases in manufacturing, lack of awareness in manufacturing applications for technology long ROI and results for new implementations.
Much legacy equipment exists in manufacturing settings, and integrating new technologies with a lack of interoperability within different systems is costly and time-consuming
Over a period of time, unplanned downtime can hamper production as reliance on AI can bring complacency, with AI lacking the ability to think outside-the-box solutions, which is the USP of human intelligence in difficult situations.
Security needs and limited bandwidth from ISP’s at remote manufacturing locations hinder the move to cloud adoption and force investment in edge computing hybrid infrastructure.
How do you manage the balance between automation and maintaining a skilled human workforce in a technology-driven manufacturing environment?
Sanjiv: With a limited use case available in automation in a manufacturing environment along with a crunch of skilled manpower, we take help from external consultants for solution design with continuous involvement of our teams, get the solution implemented and train teams throughout the process for operations and model teaching, fostering learning culture which ensures that the workforce remains agile and ready to embrace evolving technologies.
What emerging AI trends or technologies do you believe will have the most transformative impact on automotive manufacturing in the next 3-5 years?
Autonomous driving, prescriptive maintenance, and sustainable practices are becoming a reality with AI transforming the manufacturing process by automating manufacturing through robotics and enabling real-time data collection and analysis, leading to faster decision-making, streamlining production and enhancing quality control.
AI reduces the time required for design approval and sanction by enabling a quicker and better design workflow. Additionally, AI aids manufacturers in producing a variety of designs for improved product concepts and processes for autonomous vehicles, simulations on crash tests, product fitments and looks.
With more and more advancements and adoption, new ways of AI implementation will emerge, changing the views we look at today.
How do you see technologies like digital twins, machine vision, or generative design influencing the way manufacturing processes are optimised?
Sanjiv: By embracing digital twins along with AI, IIOT, VR one can gain deep insights into operations, improve decision-making, and enhance productivity through the creation of a virtual sandbox of their plant instead of investing in assets for trials having multiple iterations.
Computer/machine vision systems are a technology that enables machines to perceive, analyse, and interpret visual information from the surrounding environment.
It involves the use of cameras or other imaging devices to capture images or videos and then applying advanced algorithms and techniques to extract meaningful information from these visual inputs, having wide implementation in quality inspection in manufacturing, Robotics and automation, object recognition, safety, medical imaging and prescriptive remedy, In Agriculture, gaming and training.
Generative design is an innovative approach that involves using algorithms and artificial intelligence (AI) to generate multiple design options based on specified parameters and constraints.
Designers can explore numerous design alternatives quickly and efficiently. Generative design tools typically generate a multitude of design options, which can then be evaluated based on specific criteria, complex geometric shapes and structures that may be difficult to conceive manually can be done easily. These designs can leverage the full potential of advanced manufacturing techniques such as additive manufacturing (3D printing).
Lightweight products and components lead to material savings, competitive advantage through accelerated innovation and faster design, prototype and bring a product to market faster through improved efficiency by enabling multiple processes to take place simultaneously instead of traditional sequential processes.
It will fasten the use of additive manufacturing by creating complex designs for pilot projects till the cost of additive manufacturing is reduced to have full small lot productions.
How do you ensure responsible AI adoption in your organisation, particularly in terms of sustainability, data privacy, and fair practices, while scaling AI in manufacturing?
Sanjiv: The policy is under coining as of now, but clear communication to developers, testers, their managers, and project owners has been given to adopt best practices during development and implementation. Currently, we are using them for machine data analysis where biases cannot generally happen, which is a big fear. For human-based decision-making through AI if biased data inputs are given to AI & ML then results can be an issue. Thus, a basic level of transparency must exist with respect to the development matters impacting decisions on humans like medical records, autonomous driving, Insurance claims, Loan approvals, hence a third-party audit should be done for AI itself and how it behaves. Documenting all training and test data sets, the processes used to train a machine learning AI and the algorithms used. Ensure “Explainable AI” that are sufficiently understandable to humans so that the AI’s decisions and impacts are accepted without question. On sustainability, AI’s predictive maintenance capabilities can help avoid major issues by spotting problems early, thus optimising energy consumption, extra material consumption, rejection controls through early warning on product quality deterioration etc.
Lastly, what insights or recommendations would you like to see highlighted to guide businesses and leaders in leveraging AI effectively?
Sanjiv: All the fellow CIO are capable enough to make their own decisions, but I can only say that they start with the problem to be solved, not the technology to be applied.
Choose with a focus on existing and mature AI technologies, not speculative promises or external pressures. Go for Proof of concept, start small and ramp up fine-tuning the models to have better results, All the best to all friends in the endeavour to adopt AI.
AI systems need a variety of high-quality data sources. It can be difficult to ensure that data adequately depicts the different situations that cars may face when driving, such as weather, traffic, and other factors. guarantee that AI systems operate consistently under all circumstances.